THANK YOU FOR SUBSCRIBING
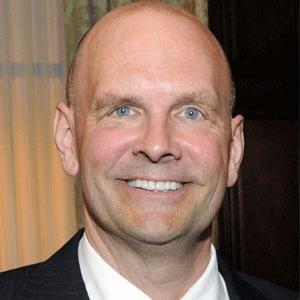
Kevin Larson, CIO, AAR CORP
AAR is an independent provider of services to commercial aviation and government customers worldwide. The company was incorporated in 1955 and today has revenues of about $1.6 billion with thousands of employees around the world. AAR combines a close-to-the customer model with a full menu of services to help customers operate more efficiently, reduce costs and maintain high levels of quality, service and safety.
AAR is traded on the NYSE under the ticker AIR. AAR is the largest aircraft repair company in North America. The CIO, Kevin Larsonsupportsenterprise applications, customer-facing business development, network& hosting infrastructures, cloud migrations and cyber security updates to the Chairman and Board of Directors.
This article will touch on several of the most pressing technology initiatives for Aerospace and many other industries which include: mobility, data analytics, along with Digital initiatives. Other on-going projects at AAR include automated inventory management programs and business intelligence with operational dashboards providing extensive visual displays across the aircraft repair and Supply chain Operations.
The aviation industry is highly regulated, FAA-controlled, driven by data and can be dynamically connected between: OEMs (Original Equipment Manufacturers), Suppliers, Partners, and Customers. Various technology and integrated solutions help the airlines compete in the competitive aviation landscape. The linkage between the aviation eco-system is connectivity, data sharing, and data collection to improve financial performance, productivity, operational excellence, and most importantly safety of flight. Safety of flight and quality are the number one objectives for every worker, company, and airline operator that support the global aerospace industry.
A key service to the airlines is having the right part, component, or exchange material when the customer has a requirement. Aviation part distributors and supply chain operations utilize demand planning and replenishment distribution software to ensure the right part is on the shelf at the right location. Several forms of automated transaction can be conducted with,“Aviation Marketplace Exchanges.” Marketplace sites bring together many different parties for collaboration on: part listings, demand RFQs, repair capabilities, and seamlessly match customer, suppliers, and repair organizations to conduct electronic and automated business.Beyond the more generic Marketplace transactions, supplier and customers
For an independent Aviation Services company like AAR, digital capabilities and integration protocols (listed above) are required to connect across the entire supply chain to provide access to operational transactions. AAR has to match numerous different customer requirements including: acceptable alternate parts, specific paperwork, packing specification, and only usecustomer approved vendors for repair operations. In the past, Airlines would fly the planes, perform the maintenance, and manage the entire supply chain. Today, many airlines have found it more strategic to focus on marketing andflying passengers in their aircraft. The business shift has expanded the need for independent aviation services companies to support the maintenance, supply chain, functions as a specialized customer service model. Along with more outsourcing for heavy maintenance checks, the Airlines are expanding PBH (power by the hour inventory management) to reduce cost and improve part availability. Strick service levels can be defined for the supply chain operations.Highly integrated PBH programs leverage a great deal of technology across integrations,customer-facing dashboards, web and mobile solution for collaboration and, in cases, marketplace sites are the primary hub used for part requisitions, provide status, and manage off unit repairs.
A future innovation would be even more automation and linkage between suppliers and customers, to avoid slow and error-prone dual data entry. Larson notes: for combined transactions, “It may be [in] the supplier system, customer system, or OEM system and it is better to automate and integrate more with web services where possible. It means better data integrity and quicker processing.”
Along with the various integration options,Business-to-Business Mobile apps can extend aviation specific functionality for customersto: shop for aircraft parts, process quotes,perform management, revieworder/shipping status, allow supplier updates on delivery dates, and approval workflows across the supply chain. Aviation Services operations span the world with 7x24 requirements where easy-to-use mobile apps add significant value for customer-facing interactions. Several examples of around-the-clock utilization for Mobile access are support for: AOGs (aircraft on the ground) and easy access to aircraft part documents such as 8130 certifications and paperwork to help release partholds frominternational customs.
Another mobility tool, best used on a tablet,provides customers with business intelligence dashboards for airframe maintenance metrics. The customer can check work-card status, work-card details and completion of milestones with real-time visibility. Further, a mobile BI solution can be used for Supply Chain customers to track KPIs and other metrics near real time. Overall the shift to mobile computing is evolving quickly and the opportunities for many aspects of aviation support will be a greatinnovation for the industry.
In closing, the aviation industry is starting to pioneer and really leverage Big data analytics to monitor on-wing performance for engines and components. Aircraft data is being collected real-time and relayed to the ground stations in preparation for necessary parts and maintenance requirements.Collecting data points on part removals by aircraft type, flight tracking (landings and takeoffs), and even weather with a range of metrics by airport location can help forecast significant events related to aircraft availability and performance. When combined, all these Big Data elements will add business value to the Airlines going forward.
At the major repair facilities data collection is also used to develop predictive analytics for non-routine maintenance operations, part and labor demands, and part reliability to reduce time for the maintenance cycle and schedule. The future of Big Data may even include non-competitive collaboration between airlines to share safety and quality events for the betterment of the entire aviation industry. The next generation of data analytics will provide significant operational and customer service value to the aviation industry.